How Furniture Makers can Optimise Furniture Production Lines
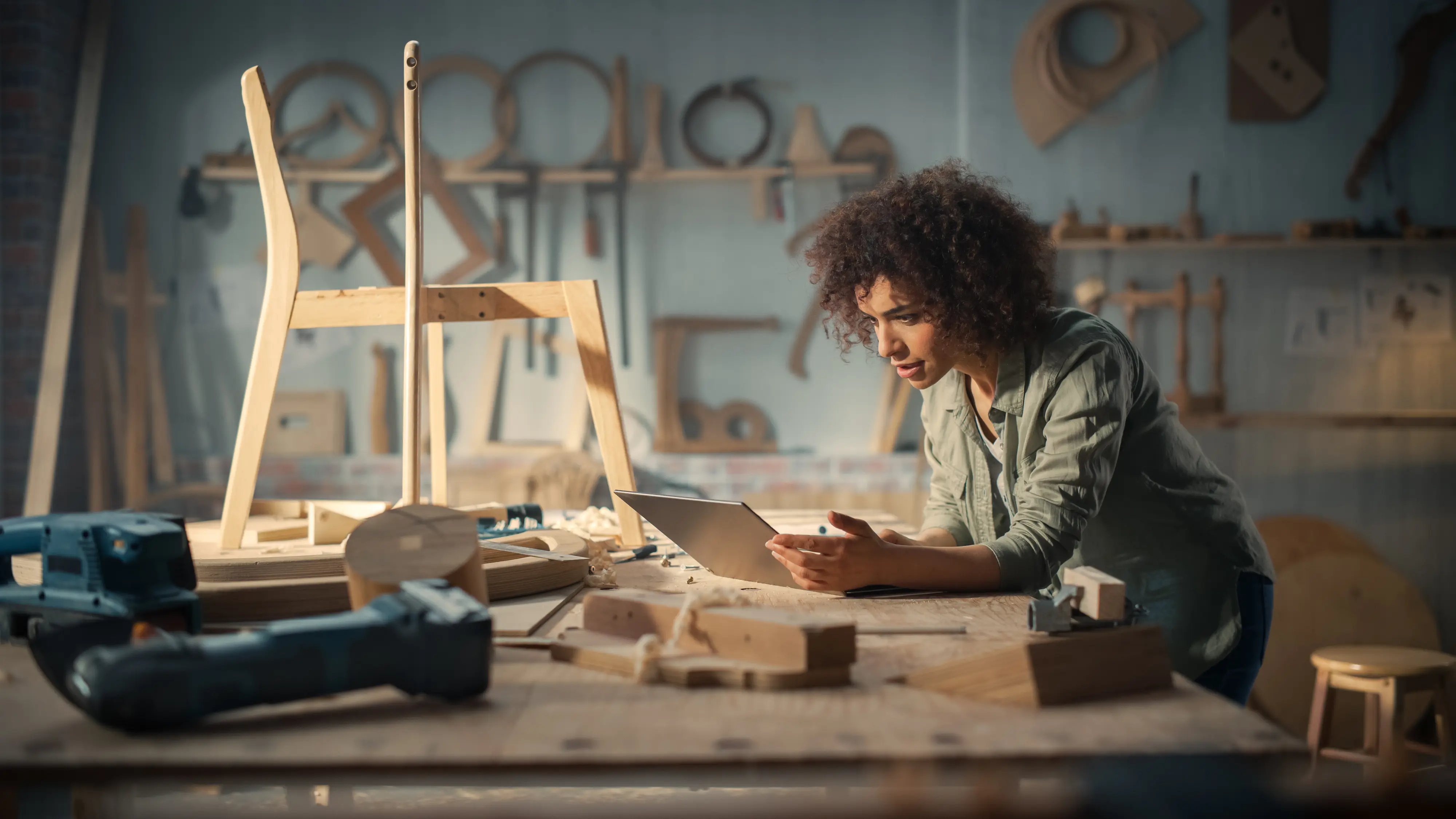
What challenges are involved in the production of custom-made wooden furniture?
It usually starts with drawing furniture in blocks (corpora). This makes manufacturing, transporting, and placing the furniture a lot easier. It’s important to specify details such as the correct thickness, connections, and denominations (structure tree) per component to prevent errors.
A designer/drawer works with complete items of furniture, while operators/furniture makers often only work with boards/panels. This means stickering with the correct names are very important. A final production can contain errors due to the (many) necessary manual operations involved. By working step by step, you can prevent these errors:
- Draw furniture in blocks (corpora).
- Specify the correct thickness, connections, and denominations per component to prevent errors.
- Use stickers with the correct names and barcodes.
- Don't forget to work step by step to prevent errors in production.
To what extent can production optimisation help furniture makers save costs?
Spotting errors early on can save a lot of time. This is especially important in preparation, because an early error often leads to extra work in the workshop. Which leads to loss of time. The often used standard rule is that 1 hour in preparation corresponds to 3 hours in the workshop.
In addition to avoiding errors, it’s also important to prevent working with old (incorrect) documents. This can lead to major problems and extra work. A good drawing program automatically saves design work with revision numbers, preventing drawings from being saved on top of each other.
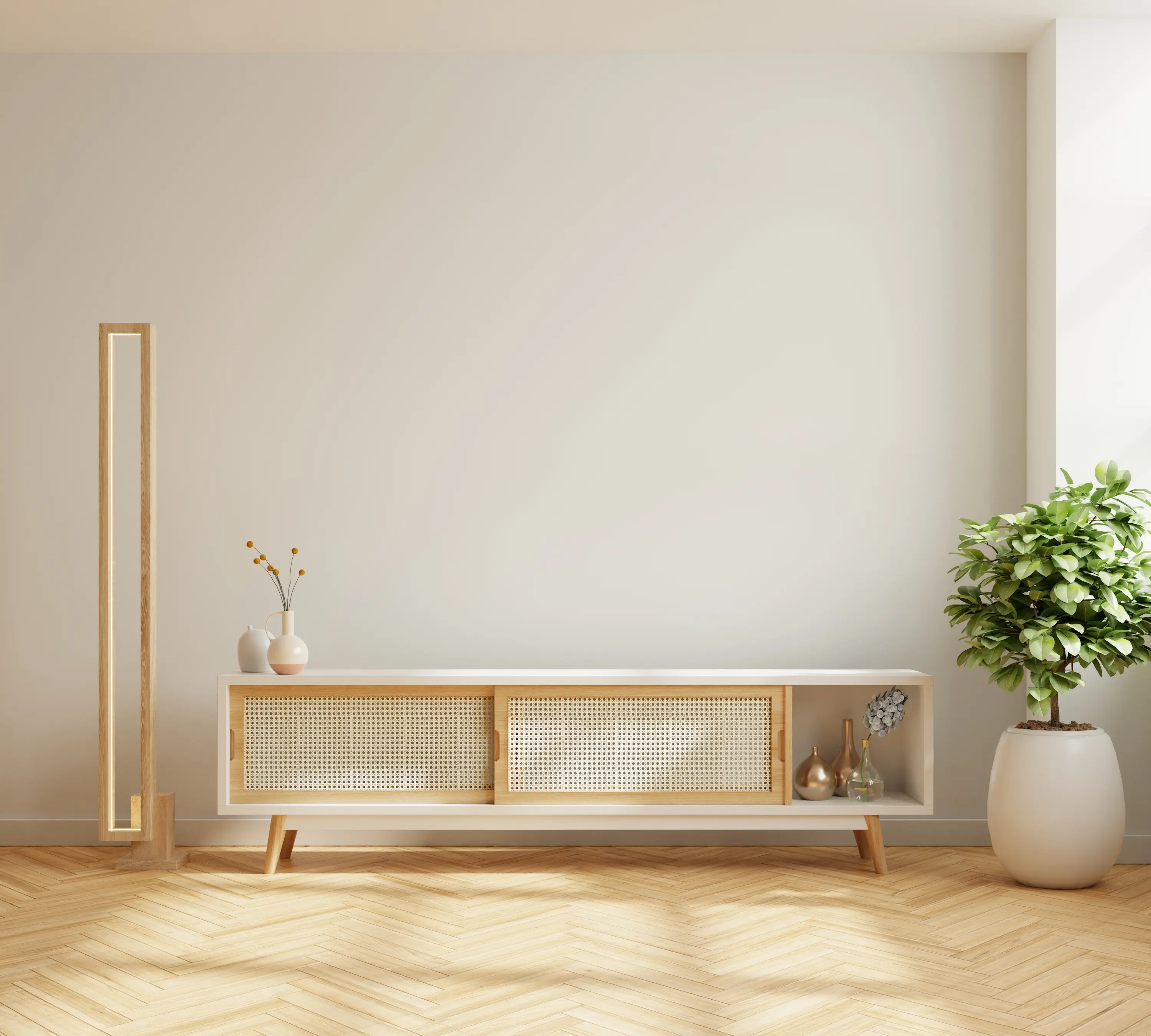
By working with a (parametric) drawing library, in which all correct documents are stored, you can save a lot of time. Meaning you don’t need to set up the furniture all over again, each time. This allows you to work more efficiently and have more extra time for other important tasks.
- Ensure good revision storage in the drawing program to prevent working with old (incorrect) documents.
- Work with a (parametric) drawing library to save time and work more efficiently.
What is the importance of effective material planning and optimisation of inventory levels?
Good material planning helps efficiently and effectively organise the materials needed for production. It ensures enough materials are available when needed, making production processes run smoothly. Fewer resources are lost due to unexpected interruptions or delays, as well.
Optimising inventory levels is also important, because it ensures companies don’t have too much or too little inventory. Too much inventory can lead to storage problems and unnecessary costs, while too little inventory can lead to delays in the production and delivery of goods.
With an ERP system, it’s easy to keep track of inventory levels, reserve materials or quickly reorder.
Ultimately, effective material planning and optimisation of inventory levels result in:
- Lower costs
- Less material usage
- Less waste
- Less use of machines
- Fewer man-hours
Literally saving costs in all areas. As a furniture maker, it’s essential to take this into account.
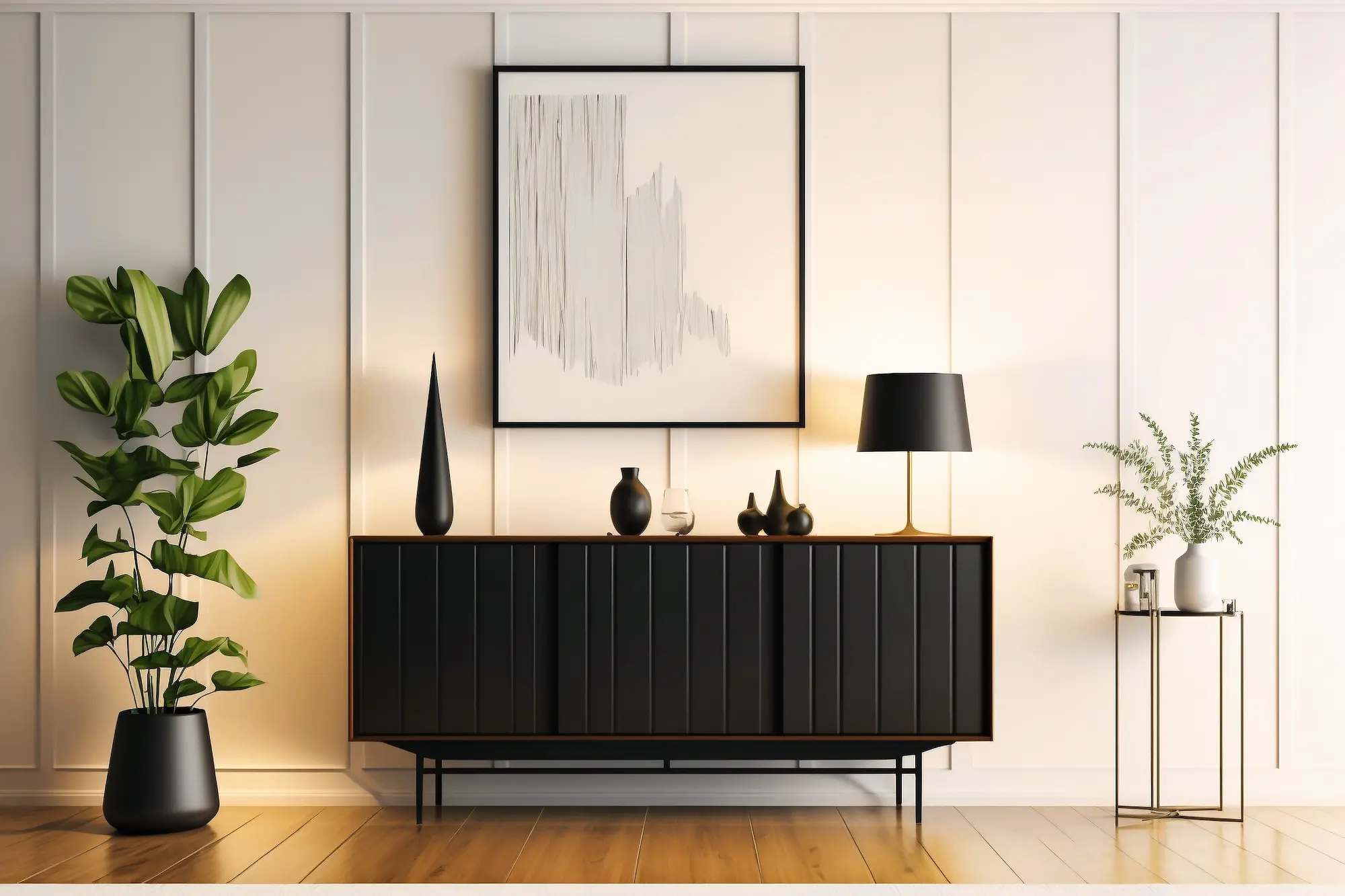
How does production planning and production control of the final product affect the final quality?
Both production planning and production control are crucial when it comes to the quality of the final product.
Production control involves monitoring the production process to ensure the product meets quality standards and specifications.
Production planning determines the production process, including the sequence of operations and the necessary materials. If this process isn’t planned properly, it can lead to inefficiencies and errors in production.
Performing checks between each step can prevent the need to remake or adjust parts. This can be done in various ways, such as through time registration, the use of barcodes, measurements, or marking off saw lists. In addition, performing sub-controls saves time and frustration in the team and prevents disappointments with customers.
Conclusion
Taking all these factors into account makes it much easier to deliver new furniture lines in time. Do you currently have a furniture project that needs to be finished on time? Upload your design and get a free quote by clicking the button below.
Find out more about our prototyping and production services here.
Related articles:
The top 3 reasons for delays in your production process and how to solve them (interior projects)
Upload your CAD file.
Get a quote.
All within 12 hours.
There’s no other wood manufacturing partner in the world that can get you a quote as fast as we can.